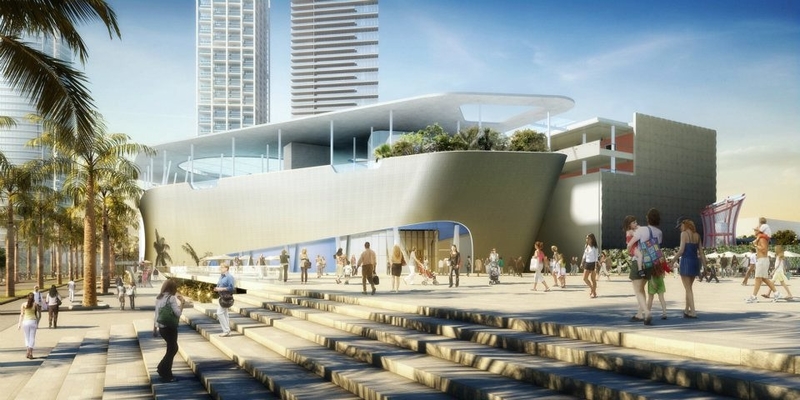
The details involved in building a new museum are seemingly infinite… especially if you are creating experiences like the Living Core exhibit at our new Phillip and Patricia Frost Museum of Science. With an aquarium that penetrates through multiple floors and includes windows on the side and underneath to provide unique views of the wildlife, the process can become very complex.
Museum COO Frank Steslow and Scott Lewis (President of project management firm Oppenheim Lewis) are responsible for many of these details. They recently met with representatives of Clax Italia, the company fabricating the acrylic panels for the Living Core exhibit. The goals were to inspect the process and confirm that all details are in place as planned, so that the panels in our Living Core will be as beautiful and perfect as they are functional.
Here is a little insight into the list of things to check off the list:
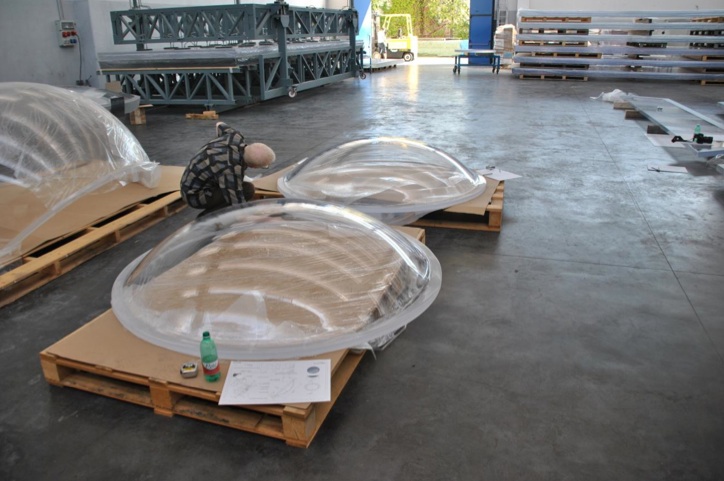
Verify the built dimensions – length, width and thickness – of the panels as compared to the architectural drawings.
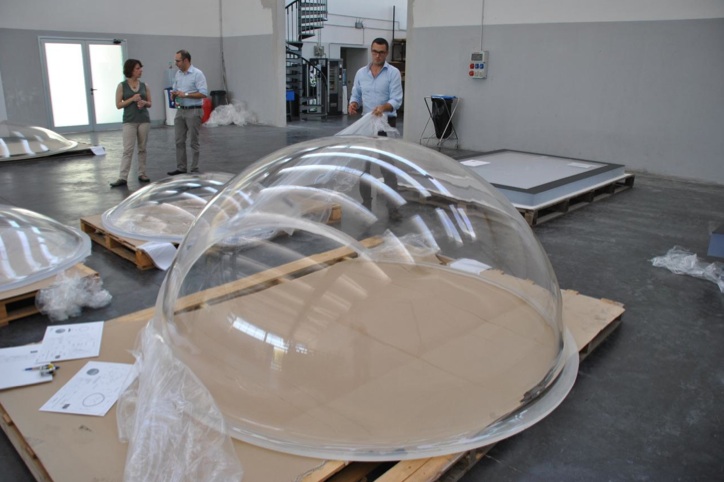
Remove the protective film and inspect panels for surface imperfections, discolorations, or internal inclusions – which refers to any foreign material trapped inside the panels
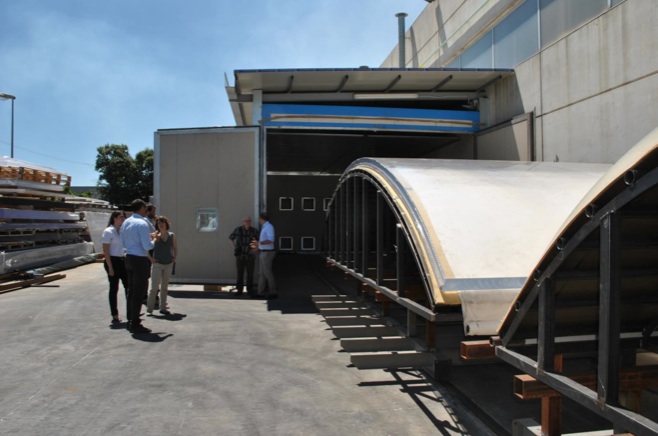
Inspect panels for distortions or asymmetries from thermoforming – the manufacturing process where a panel is heated to a temperature at which it can be formed to a given shape (here, a panel is removed from the thermoforming oven)
The next steps?
- Review production schedule, delivery sequence, installation, waterproofing, and tank testing
- Consider that the thermoformed panels will be sensitive to temperature fluctuations until they are installed and the effect is lessened by the presence of water
- Not to mention… the rest of the details for the rest of the new Patricia and Phillip Frost Museum of Science!